Above & Beyond: Customer Praises Inspection Team for Catching Undocumented Defect
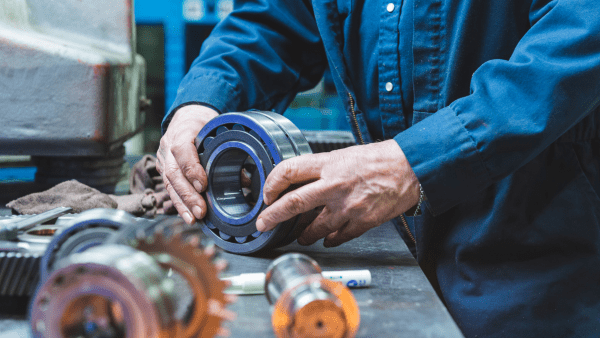
THE CHALLENGE
A misaligned bracket arm defect (not a part included in the original work instructions) was discovered during inspection, surprising the customer, as this issue had never been identified in this component before. Without detection, the defect could have led to assembly issues or potential failures in the final product. Ensuring consistent quality required a proactive approach to identifying and addressing emerging defects.
THE SOLUTION
The First Call inspection team’s keen attention to detail allowed them to spot the misalignment, preventing defective parts from moving further down the production line. The First Call team immediately reported the issue, enabling the customer to take corrective action before it escalated. The team’s expertise and thorough inspection process exemplified First Call’s commitment to quality assurance.
THE RESULT
As a direct result of the First Call inspection team’s findings, the customer immediately launched an investigation into the root cause and implemented countermeasures to prevent a recurrence. First Call revised its work instructions to include this previously unknown defect, strengthening its quality inspection criteria.
The sharp eye of the inspection team led to enhanced defect detection and prevention, reducing future risks in production. The inspection team’s outstanding performance reinforced First Call’s reputation for reliability and excellence in quality inspection services.
Want to keep up with the latest quality insights and trends? Connect with First Call for relevant news in third-party quality inspection. Follow us on LinkedIn